ポイント
-
1人とIoTを紐づけた工場の見える化で生産を効率化
-
2資材をバーコード管理し、在庫切れによる納期遅れを解消
-
3導入後は生産性が向上し、10%以上の売上アップを実現
アナログからデジタルへの転換を図り効率的な生産体制の確立へ
同社は越前打刃物の工房など、顧客ごとに仕様が異なるオーダーメイドの一品生産を中心に手がけてきましたが、近年では国内メーカーや海外にも取引先が広がって受注量が増加。特に年間を通して計画的な生産が見込める製品が7割を占めるようになってきました。
同社は2024年の創業70周年に向けた10年ビジョンの中で、アナログからデジタルへの転換による生産性の向上をミッションのひとつに掲げました。その取組みとして、発注情報から在庫管理、工程設計、工場の稼働状況や生産進捗、生産実績のデータをIoT技術で集積し、AIに学習・分析させて受注量の予測を行うシステムの開発に着手。予測に基づいてある程度の量を生産しておき、注文に応じて割り当てていく見込み生産と従来の受注生産を両立するハイブリッド型の生産体制を目指しました。
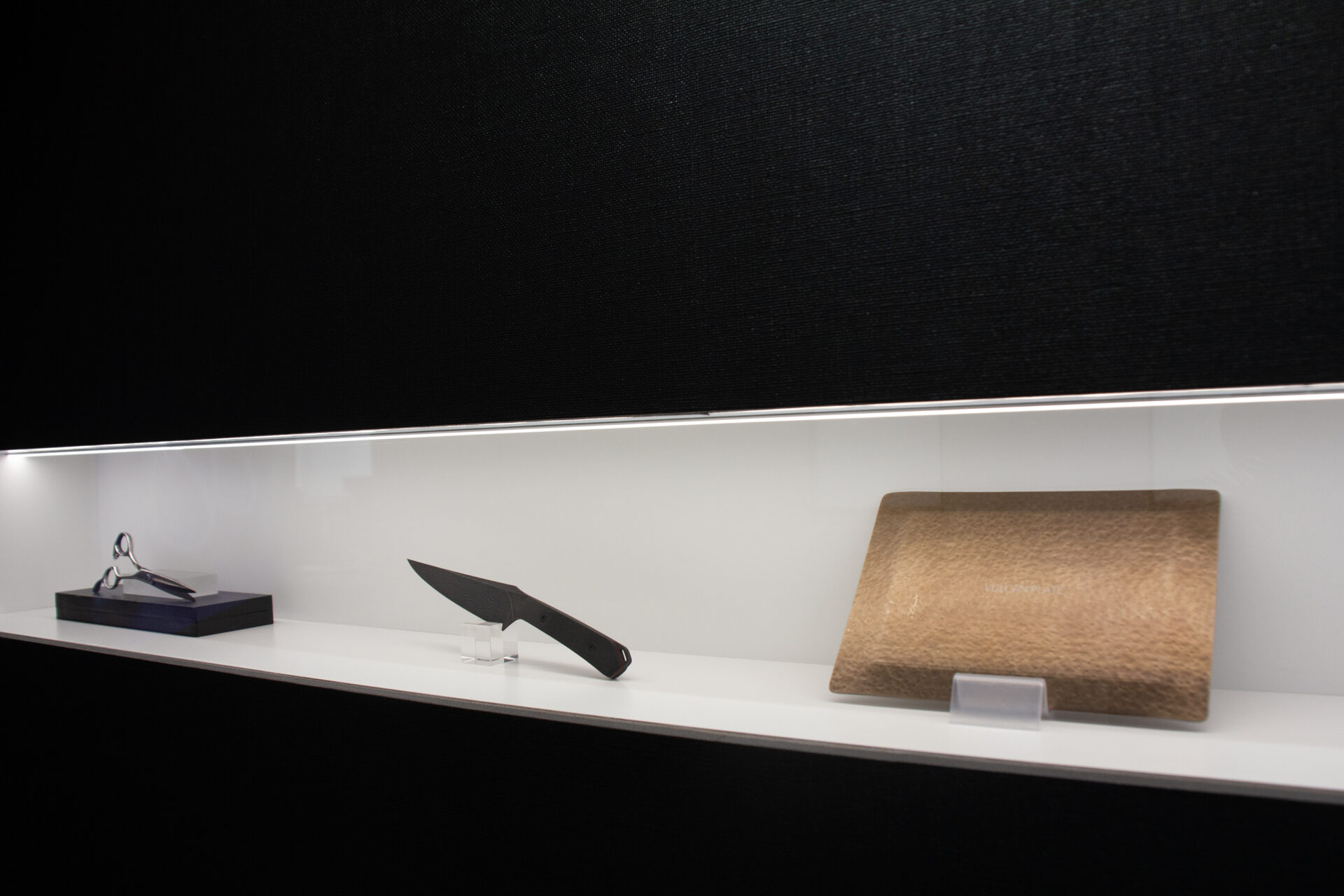
工程ごとの作業時間と資材の在庫をデータ管理して見える化を図る
工場で課題となっていたのは、受注生産品の製造時に起きる段取り替えでした。受注品目ごとに金属の接合にかかる熱処理の設定が異なるため生産の停滞が発生しやすく、進捗管理は現場リーダーの経験任せになっていました。そこでまず、見込み生産の製品群をカテゴライズし、受注情報や工程の進捗なども一緒に管理できるデータベースを作成。工場の機械はアナログ型のものが多かったことから人とIoTを紐づけ、工場スタッフにタブレットを支給して各工程にかかる作業時間を見える化する方法をとりました。同社で使う資材は納期に1年近くかかるものもあり、見込み生産の運用には適切な資材管理も欠かせません。そのため資材はすべてバーコード管理に切り替え、資材切れによる納期遅れを起こさない体制に整えました。
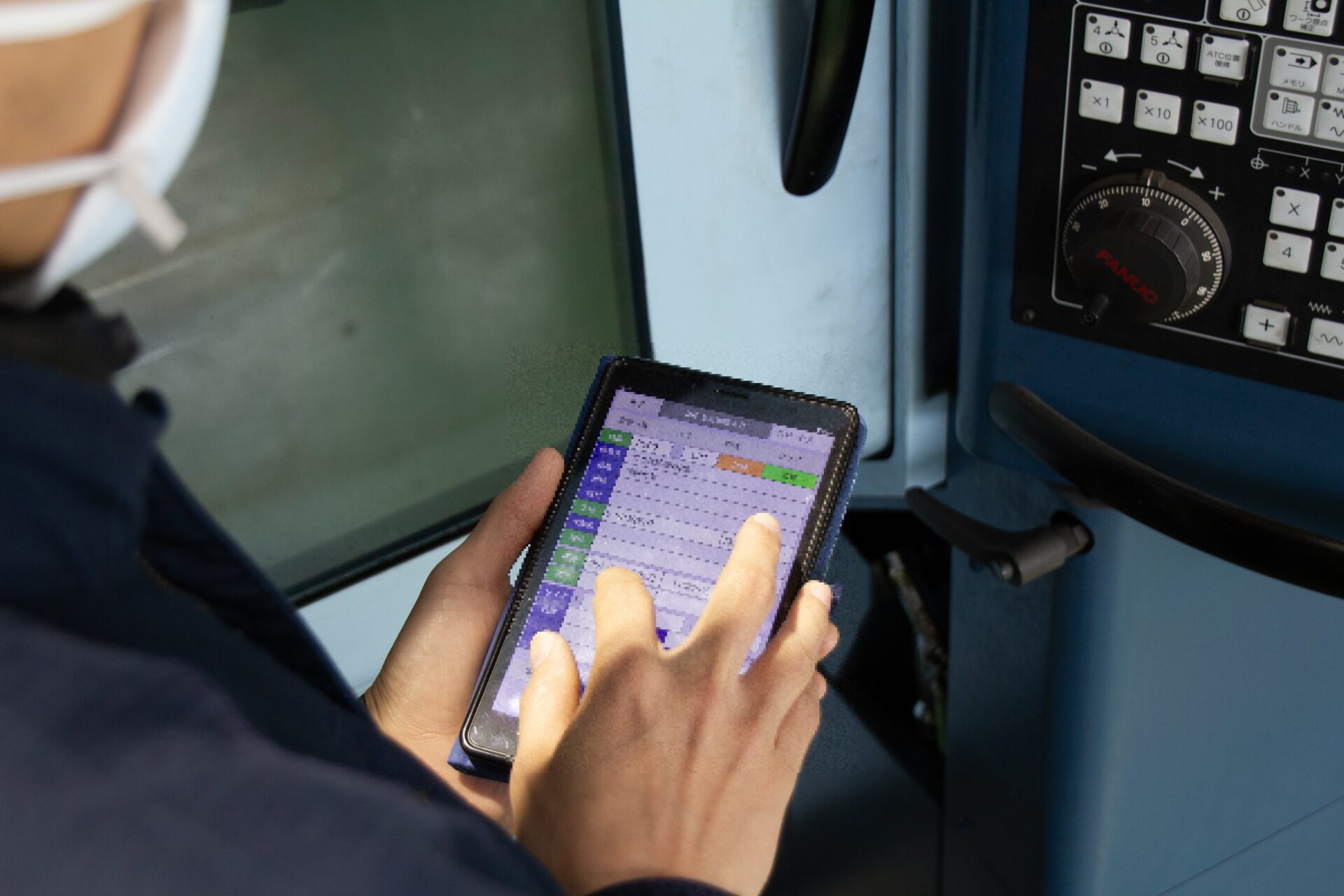
働き方改革と生産性向上を両立
工場ではスタッフが作業の開始時と終了時にタブレットの画面をタップすると、所要時間が計算され、システムにデータが蓄積されます。工程ごとに製品の重量も記録され、どこでロスが起きたかも分かるようになっています。工場の稼働状況や生産実績が数字で俯瞰できるようになったことで、目標の生産量を達成するためにどう人員を動かすかを考えたり、いつもより時間がかかっているのは何故かをすぐ確認に行ったり、リーダーが動きやすい環境になり、生産の流れがスムーズになっていきました。
「過去に最高売上高を計上した年は2交代勤務で達成しましたが、ハイブリッド生産体制に移行後は同じ売上高を通常の日勤のみで実現しました。売上高も導入前の10%以上伸びており、現場の負担を抑えながら生産量を増加できています」と胸を張る坪川氏。当初は集積したデータの分析にAIを活用する方向でしたが、現状ではBIで十分運用できているため、蓄積されたデータをどうAIと結びつけて業務改善に活かすかが課題だと語ります。
今後の展望
当社は2025年に新工場の稼働を予定しており、生産能力はこれまでの2倍以上になります。現在、刃物以外の新市場の売上高は全体の10%程度ですが、年20%の成長率で拡大しており、高度な技術を求める研究機関やメーカーからの依頼も増え続けています。その中で取り組んだハイブリッド生産体制への移行は納期管理のクオリティ向上にもつながり、新市場開拓への大きな自信になりました。新工場が稼働すれば人員が増え、今まで以上に生産管理が重要になってきます。そこでも見える化されたシステムが効果を発揮すると期待しています。(取材者:取締役常務 坪川 翼 氏)
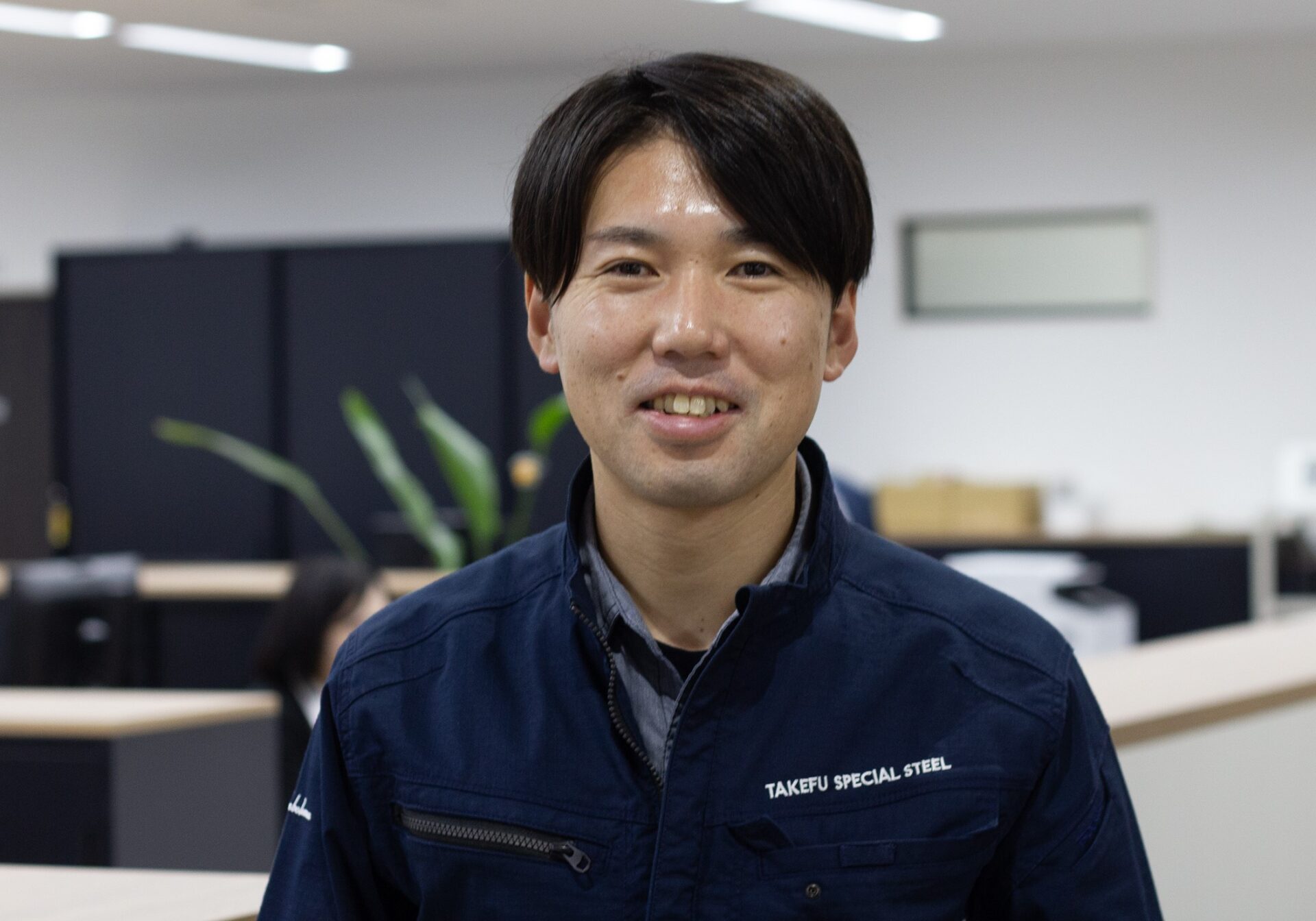
取り組みにかかったコスト
コスト | 非公開 |
---|
相談先
相談先 | 令和元年度IoT・AI・ロボット等導入補助金を活用 |
---|
会社概要
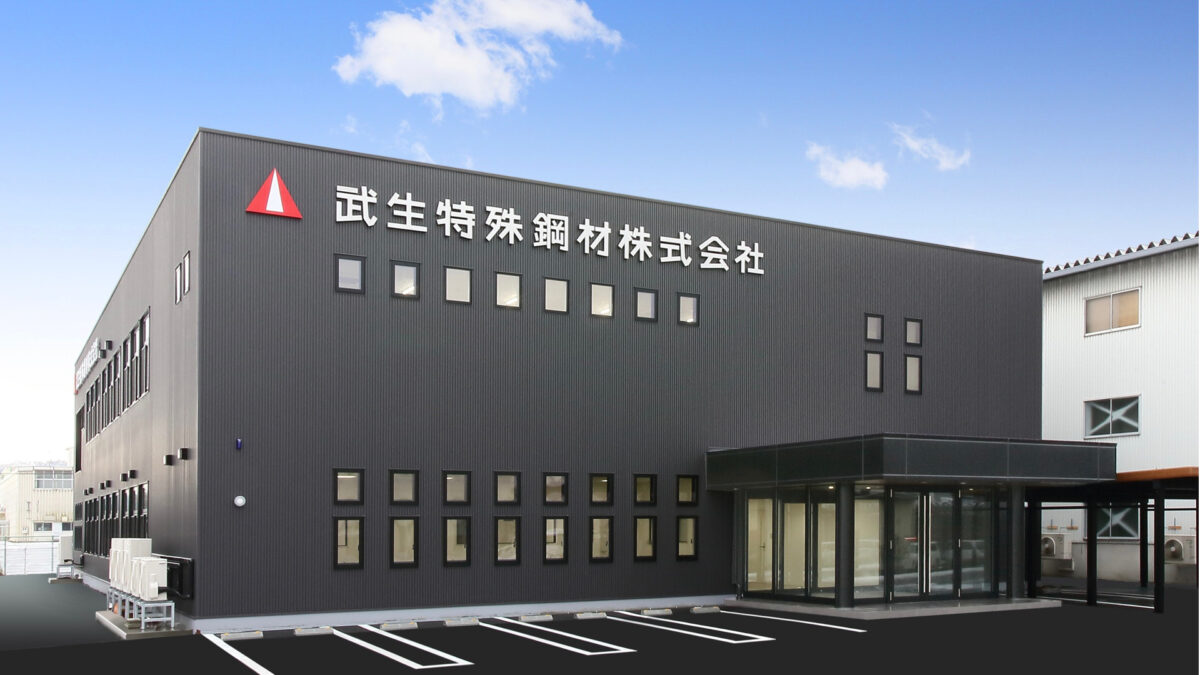
社名 | 武生特殊鋼材株式会社 |
---|---|
代表者 | 河野通郎 |
所在地 | 越前市四郎丸町21-2-1 |
従業員数 | 58名 |
取扱品目 | クラッドメタルの受注生産販売、オリジナル刃物鋼「V鋼シリーズ」、金属受託加工、クラッドアート |