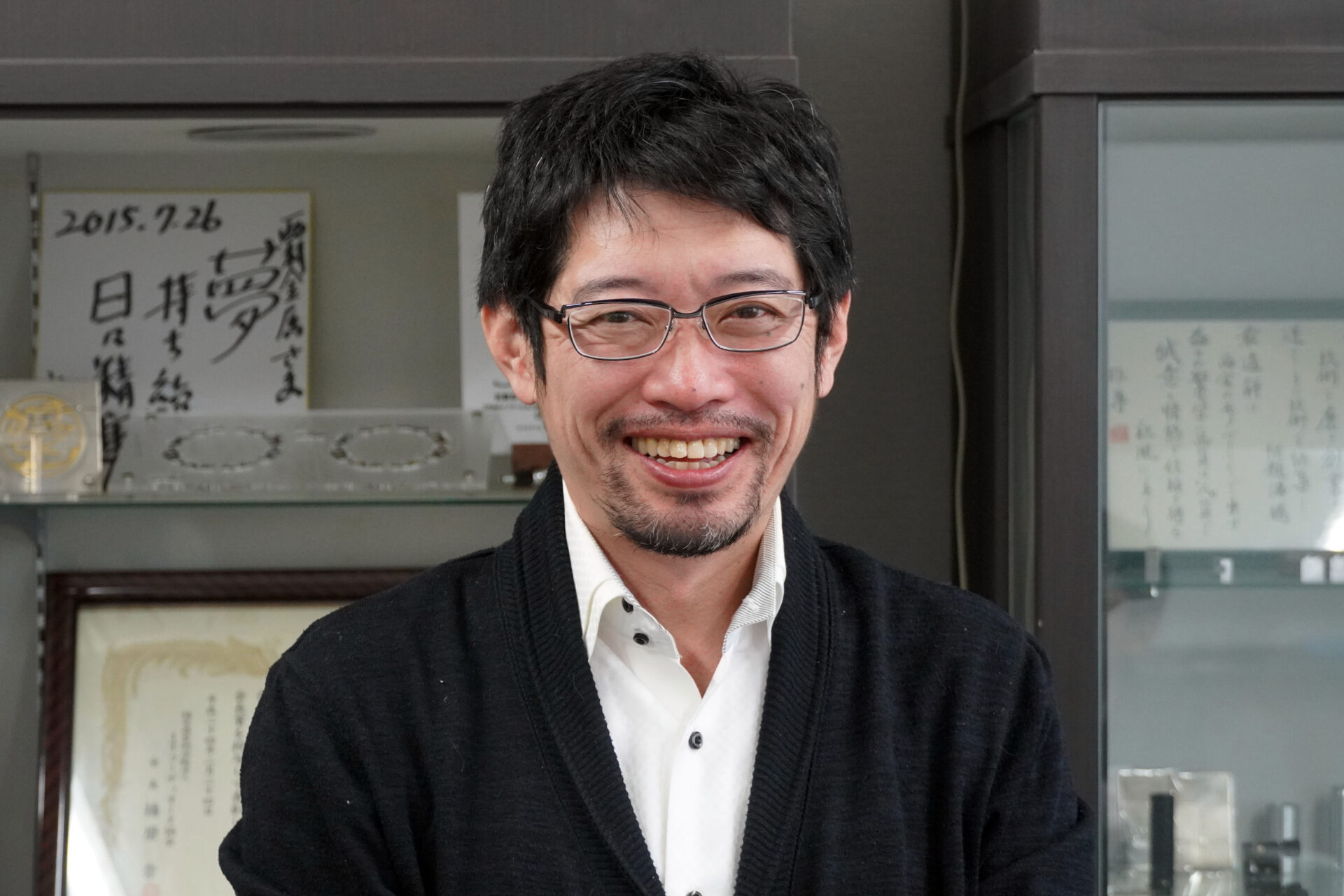
膨大な基礎データ生かし良品判定基準を明確化
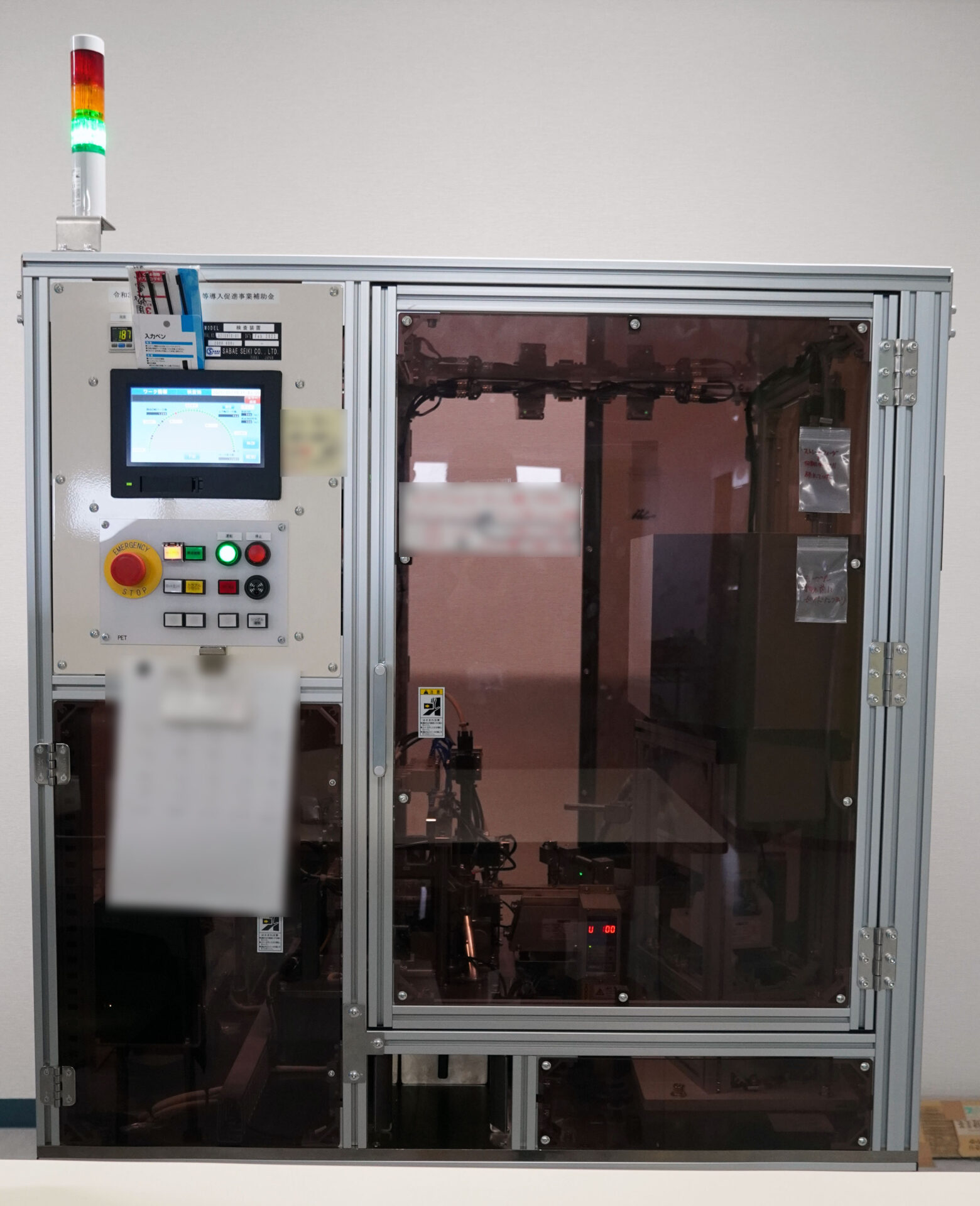
2000年にウェブサイトを開設するなど、かねてから積極的なIT投資を続ける同社。サイトからの受注も含めて現在、月当たり30万~40万個の精密部品を製造しています。大ロット受注も少なくありませんが、検品にかかる人手増による判断のばらつきが課題となっていました。
そこで着目したのが、カメラや画像解析プログラムなどからなる外観検査システムの構築。一つ一つの精密部品を撮影し、傷や打痕などの有無を数十ミリ秒で判定した後、不良品を選別する機能を備えます。
「良・不良の基準を覚え込ませることで、感覚的にもなりがちだった判定基準が明確になりました。良品の規格化につながり、判定基準を取引先と共有できるようになったのもよかったです」と西村氏は話します。
AIによる検品には膨大な基礎データが必要です。システム構築の背景には月産数十万個の実績があったからで、西村氏は「多品種小ロットの検品だとAIの導入は難しいのでは」とも話します。
社員間の連絡密にするチャットツール導入も
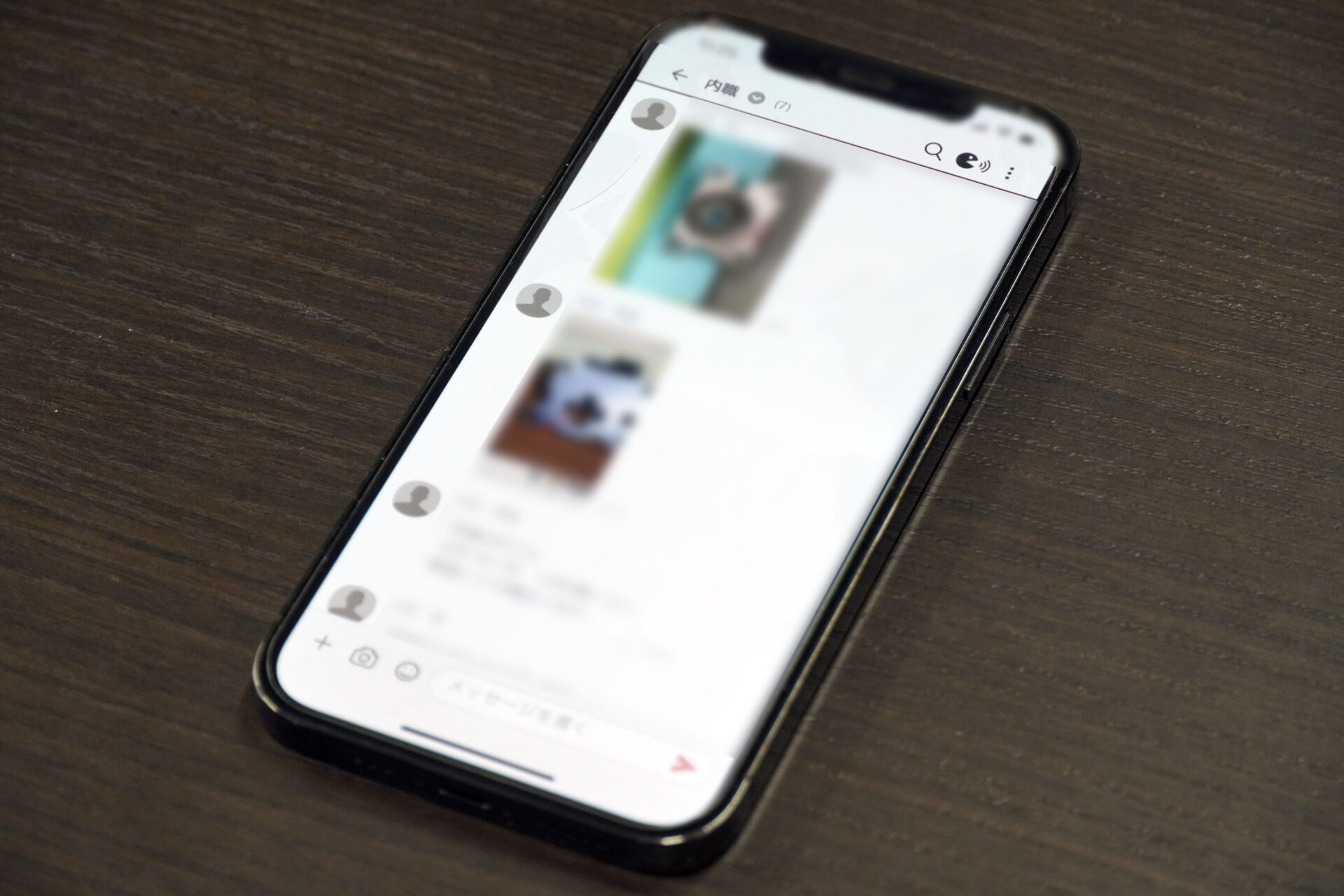
DXによる省人化は人員配置の適正化につながる一方、情報共有ができていなければ社員間の連携不足を招きかねません。そこで、同社ではチャットツールを導入し情報共有を密にする取組みも進めています。
導入したのは「エルガナ」というツール。ビジネスチャットに特化しており、フリープランでも制限なくIDをつくることができたり、写真添付の投稿ができたりする特長を持ちます。
検品担当の内職チーム5人にもツールを展開し、発見した不良品の写真をチャットに投稿するなどスピーディな情報共有を実践。情報は検品を統括する社員にも即座に共有され、検品時間の短縮につながっています。
DXが話題となる以前からIT活用による業務改善に力を入れてきた同社。社内には2006年からのビッグデータが蓄積されているそうです。「会社はデータを蓄積する場所。データ処理は外注化もできますが、元のデータがなければ事は始まりませんから」と西村氏はDXのポイントを語ります。
先代の西村忠憲氏から会社を引き継いで10年という憲治氏は、「これまでのIT化の取り組みには失敗事例もたくさんありました」と苦笑いします。
「日々の暮らしもDXによるさまざまな変化が起きていて、ものづくりのDXはもはや避けて通れなくなりました。自動化できる作業とはすなわち、日々繰り返し行っている作業。それを見極めた上で省人化に取り組むのがDXの第一歩ではないでしょうか」と話します。
会社概要
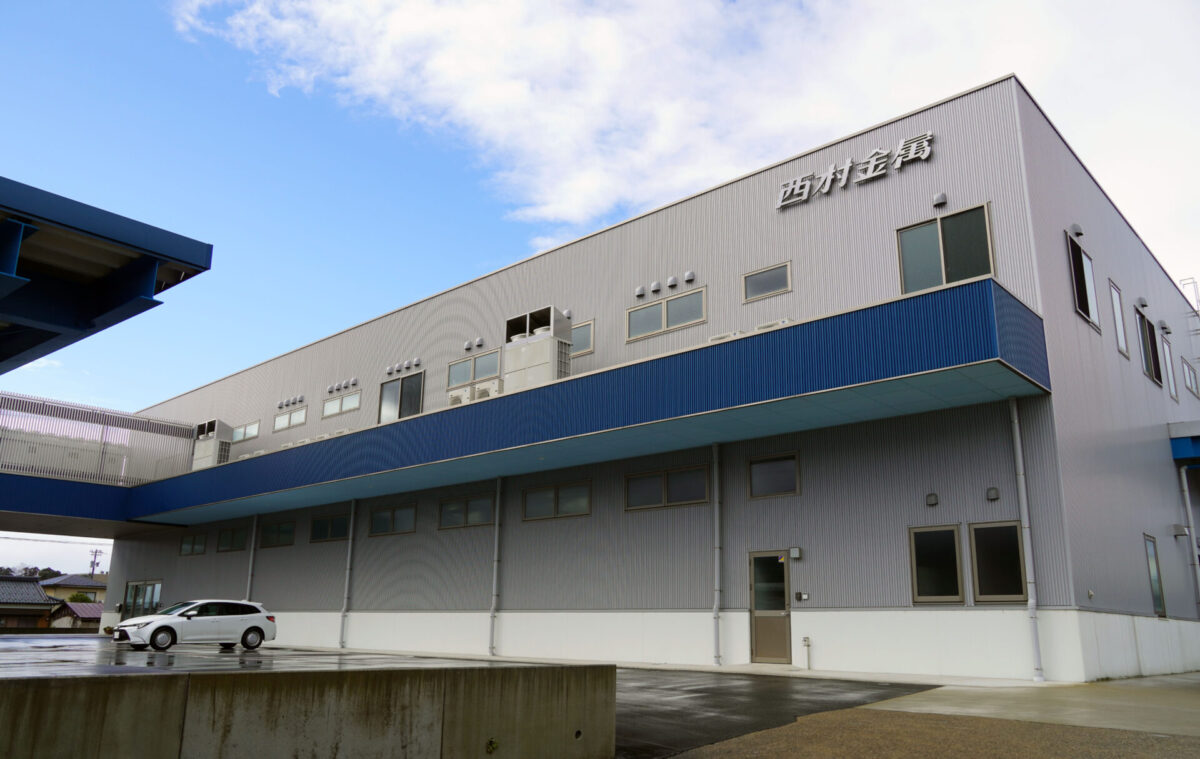
事業所名 |
株式会社西村金属 |
---|---|
所在地 | 鯖江市丸山町3-5-26 |
代表者 | 西村憲治氏 |
資本金 | 1500万円 |
事業内容 | 眼鏡部品製造販売、精密部品加工 |
従業員数 | 32名 |
TEL | 0778-51-2348 |
HP |