ポイント
-
1正確な試作品が製造できるとともにトラブルが激減し、納期も大幅短縮
-
2新技術への挑戦が取引先の信頼を生み、眼鏡フレーム製造に事業を拡大
-
33Dプリンターによる金型製造など、新規技術の研究開発にも意欲的
眼鏡の産地鯖江で最初に3Dプリンターを導入
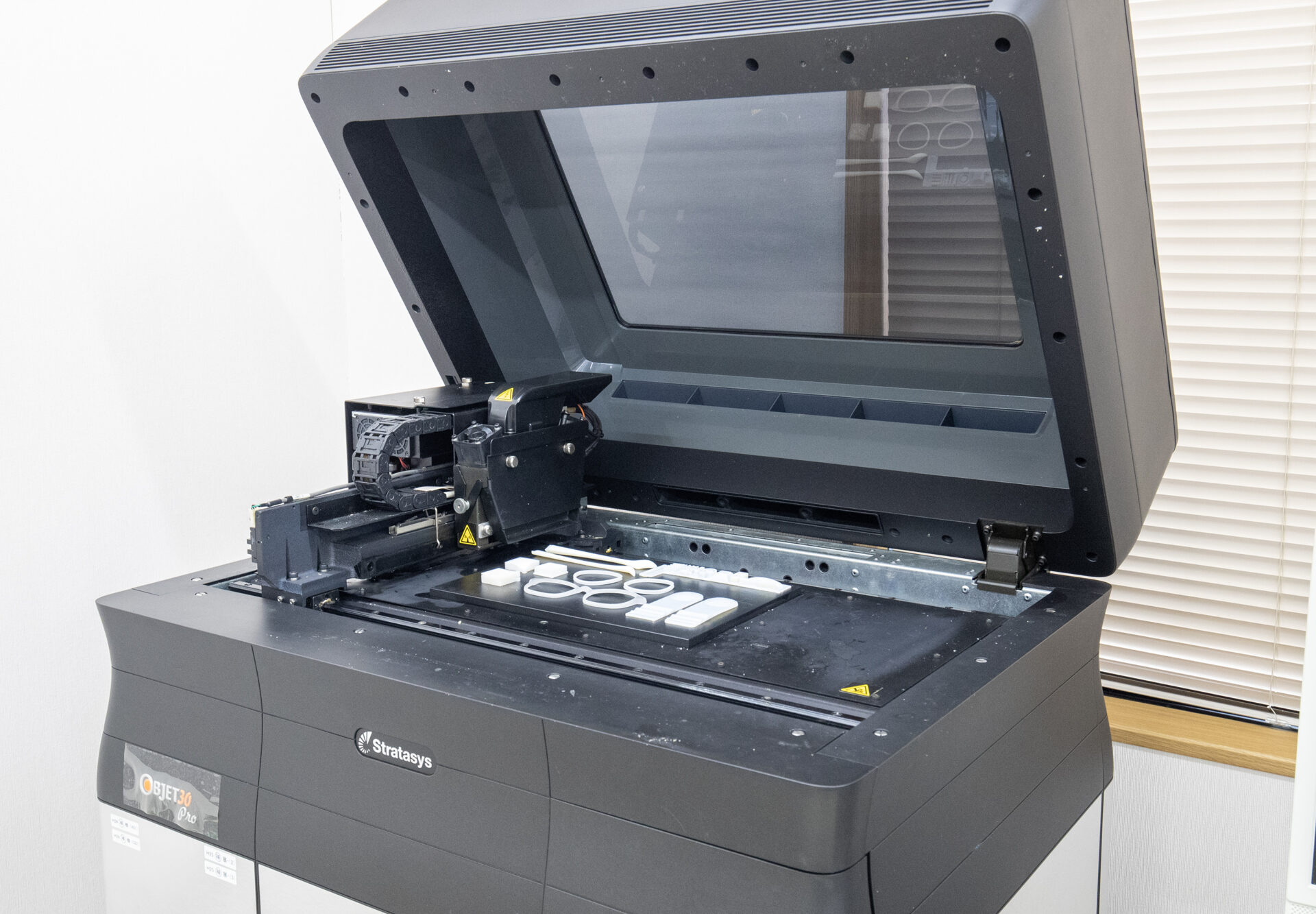
2013(平成25)年、新技術による競争力の強化を図ろうと、眼鏡の産地鯖江としては最も早く、試作品の製造工程に3Dプリンターを導入。プラスチック製眼鏡のフレームのフロント部分やテンプルなどの試作品作成に活用しています。
試作品は従来、手作業の削り出しで製作していましたが、3Dプリンターを使うことでCADによるデザインデータから自動的かつ正確に、複数同時に製作できるようになりました。設計との誤差がない試作品を実際に顔にかけて装着感を確かめることができ、金型の修正などのトラブルが激減しただけでなく、納期も大幅に短縮できました。
さらに、先駆的な取組みが取引先から高く評価され、従来の金型製造と眼鏡部品の製造に加え、大手眼鏡量販店向けのOEM用の眼鏡フレーム製造にも事業範囲を拡大するきっかけとなりました。
3Dプリンター活用の課題解決には、技術的基盤が不可欠
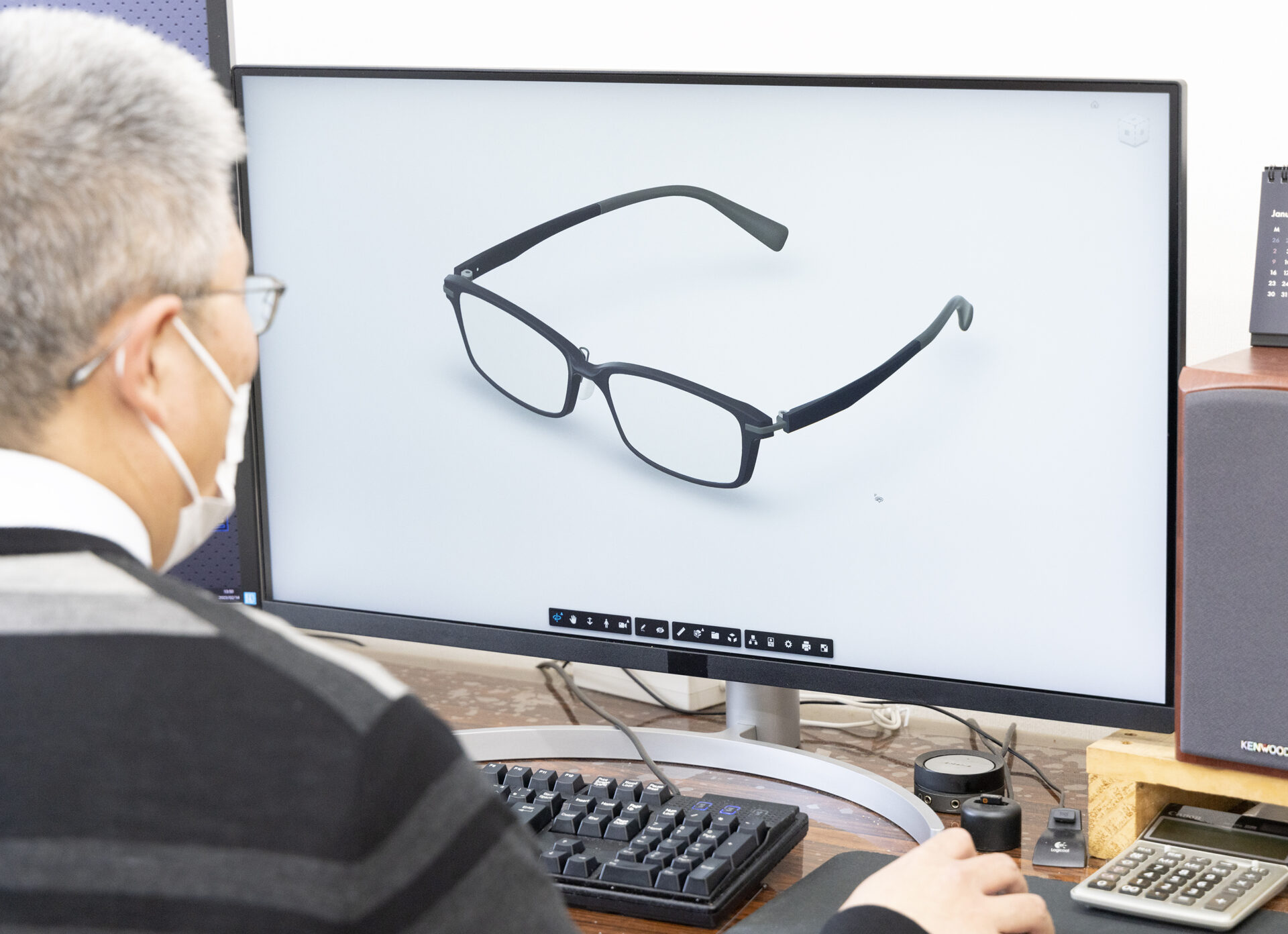
3Dプリンターの導入には国のものづくり・商業・サービス生産性向上促進補助金を活用。併せて3Dスキャナーも導入しました。機器の運用は自社内の技術者が担当。試作品の製造には素材の選定や、強度の確保などの多くの課題がありましたが、CADによる三次元設計のノウハウや、金型やプラスチック成形で蓄積した既存技術が課題解決のベースとなりました。
玉田隆則社長は「スキャンしただけで簡単に望む製品が製造できるわけではなく製造の条件を整えるのが大変です。活用には専門的な技術的裏付けが不可欠」と強調。「短期的には困らないが、いざ3Dプリンターが標準技術となった時に、使い始めようとしても工法への理解や活用という点のノウハウを蓄積していないと競争力が弱く『時すでに遅し』となる」ことを懸念しています。
機能性眼鏡や金型製造にも、活用範囲を拡大
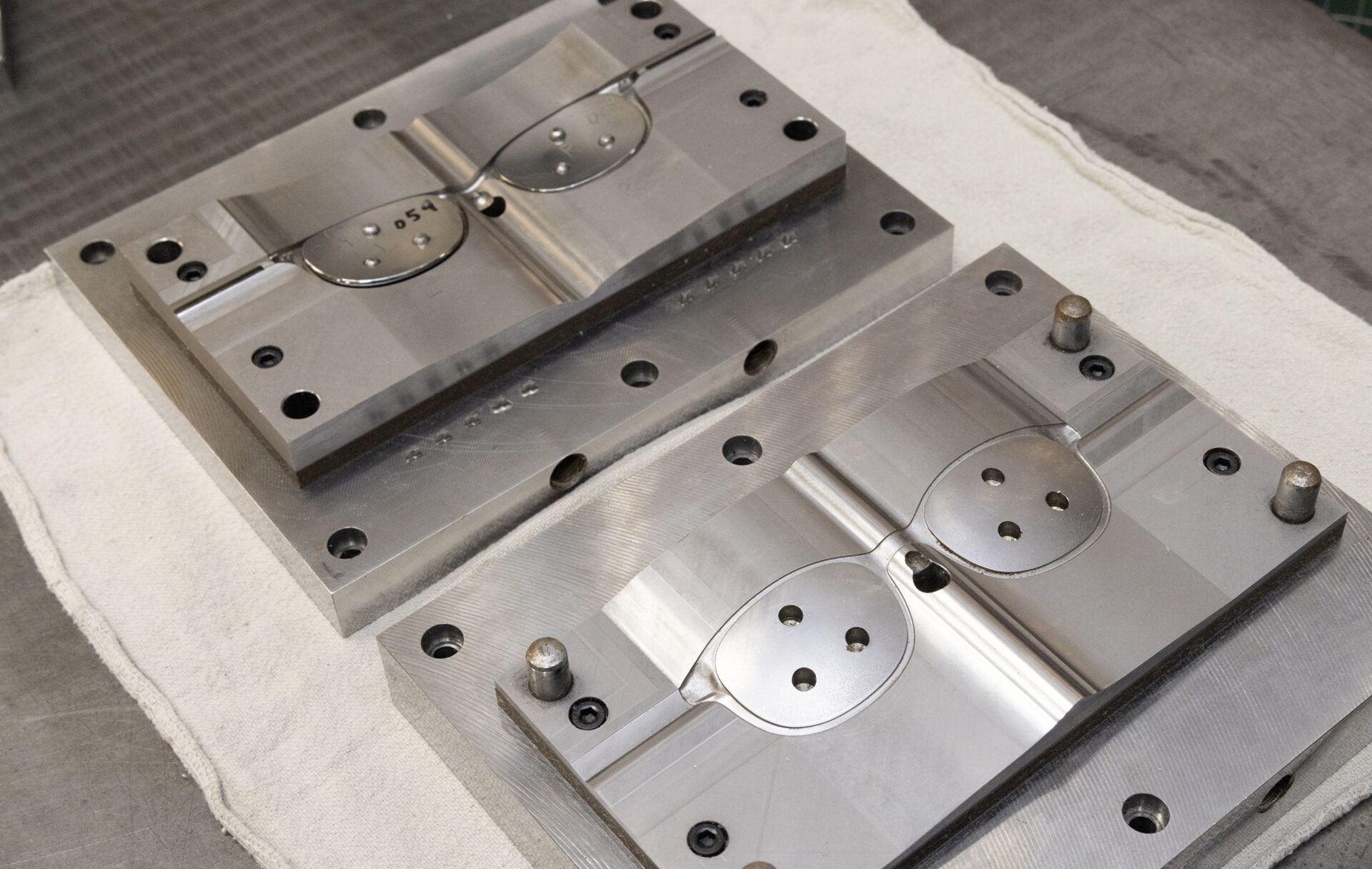
造形の自由度が高い3Dプリンターの特性を生かし、国立情報科学研究所との共同研究で、樹脂による一体成形で「カメラの顔認証を防ぎプライバシー保護する眼鏡」を開発。2018年の「はばたく中小企業・小規模事業者300社」に選出されました。
さらに2020年には、社内の製造現場と社外の顧客やデザイナーが、クラウドベースでCADデータなどの情報を共有できるように生産システムを変更しました。
同年には近畿経済産業局の積層技術を生かしたモノづくり「Additive Manufacturing(AM)」の検証事業「Kansai-3D実用化プロジェクト」のモデル企業に選定され、福井県工業技術センターや、株式会社 松浦機械製作所と共同で、3Dプリンターを用いて樹脂フレーム金型を金属粉末積層で造形する研究を行っています。
今後の展望
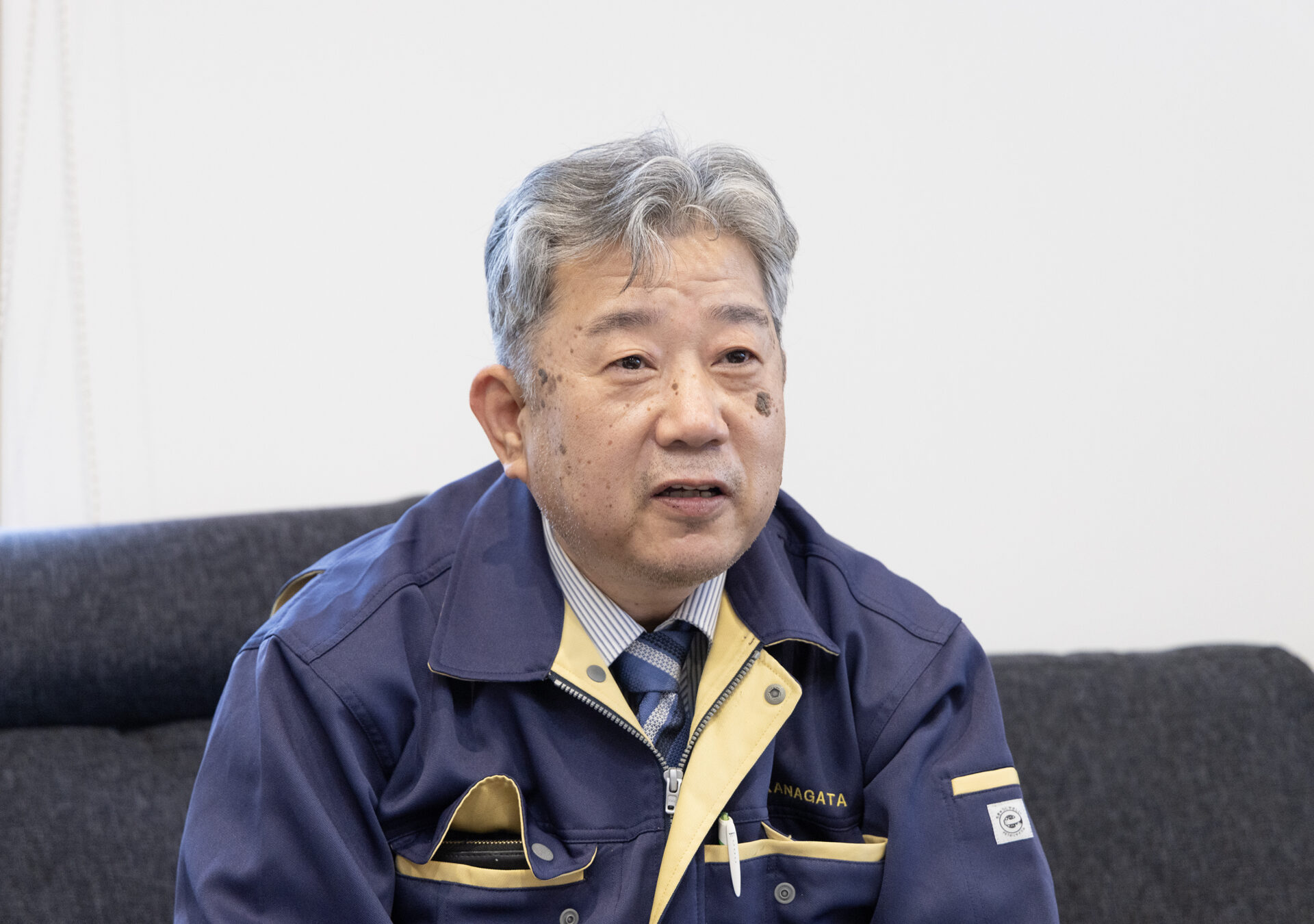
3Dプリンターによる金型の製造は、金型開発でも技術的な選択肢となる可能性が高く、引き続き強度などの検証を行っています。こうした金属造形加工技術の活用は、眼鏡産地鯖江の課題となっている機能性眼鏡による価値創造に寄与できるものです。従来の視力補正用だけでなく、工場用の防塵眼鏡などのセーフティ分野や医療用ゴーグル、視聴覚機能を拡張したウェアラブル端末など、高付加価値な製品開発の可能性を追求していきます。
取組みにかかったコスト
コスト | 1300万円(補助金活用) |
---|
相談先・業務委託先
相談先 | 3Dプリンター代理店商社 |
---|
会社概要
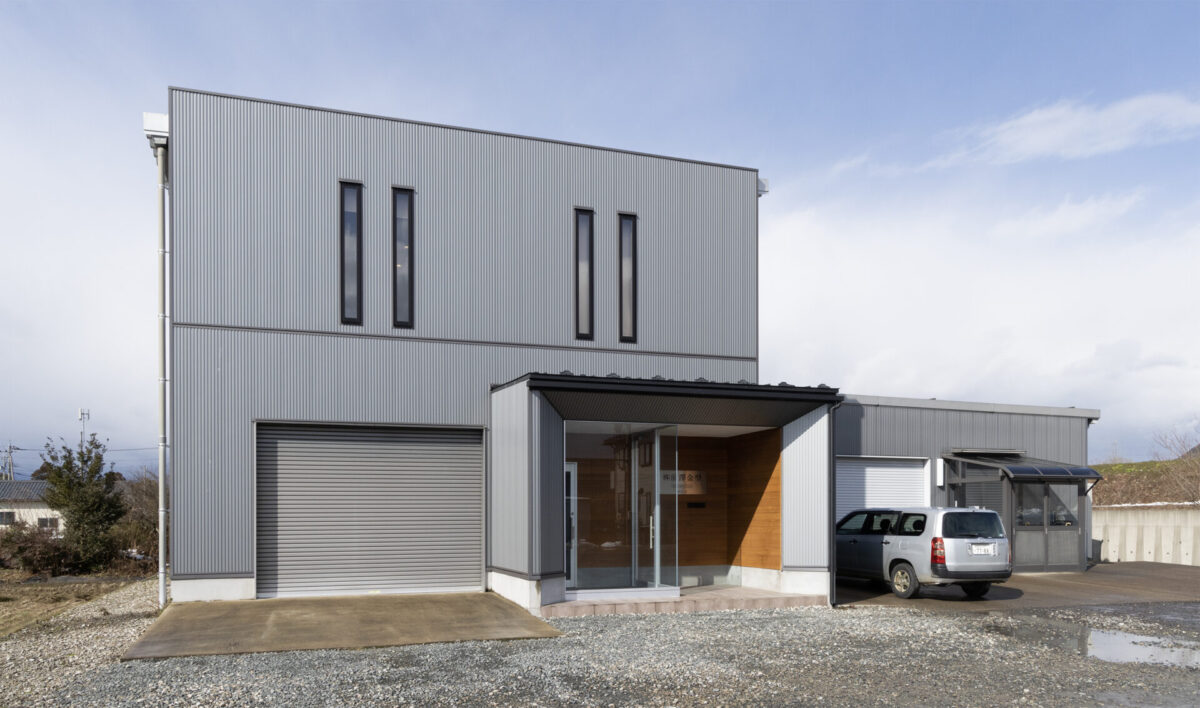
社名 | 株式会社 前澤金型 |
---|---|
代表者 | 代表取締役 玉田 隆則 |
所在地 | 福井県鯖江市石田上町51-11-1 |
従業員数 | 10人 |
業種 | 金型の製造販売 眼鏡枠および眼鏡用部品の製造販売 上記に附帯する一切の業務 |